Professional injection molding factory
- Rapid Lead Times
- 100+ Materials for Choosen
- Strict Quality Control System
- On-demand Production
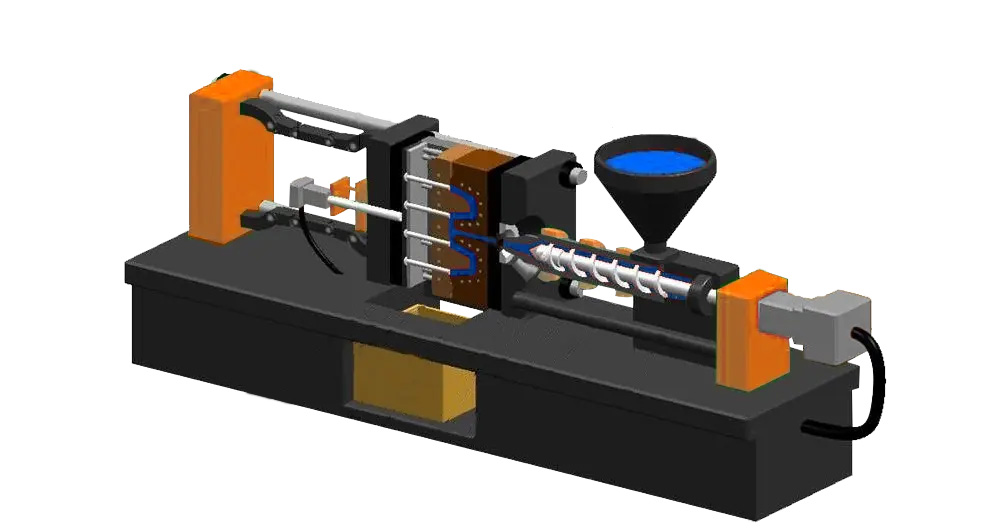
Plastic injection moulding services:
Delivering precision plastic parts
Injection moulding services to manufacture high quantity production parts and custom on demand injection moulded parts.
Your trusted injection moulding experts
Injection moulding services suitable to manufacture plastic parts high to low volume ensuring repeated geometrical and visual properties. With years of experience in the industry, we have established ourselves as a leader in delivering precision and excellence.
Our team is dedicated to transforming your product ideas into real products. Using the magic of injection moulding, we streamline the production process to ensure consistency in producing technically correct parts. From small components to larger, complex designs, our state-of-the-art equipment and skilled technicians can handle it all.
We take pride in our moulding versatility. Our injection moulding services cover a wide range of plastic parts, allowing us to meet your unique needs. Whether you require prototypes in intricate designs, or developing injection moulds for scaling to production in specific materials, our experience ensures that we can produce the perfect parts at speed for your application.
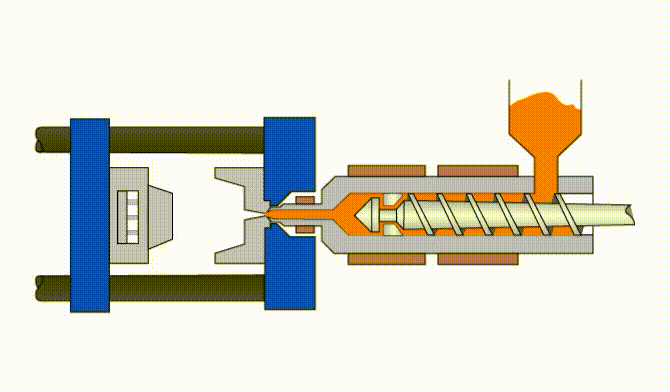
Industries We Serve
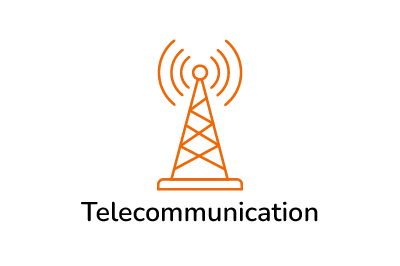
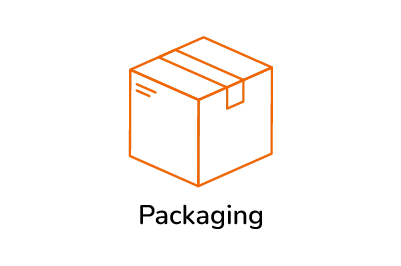
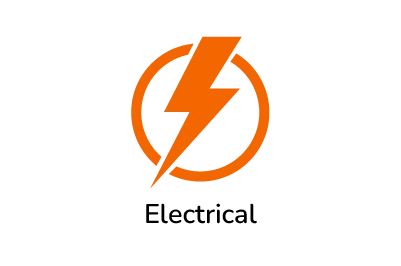
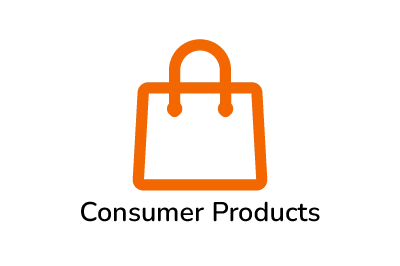
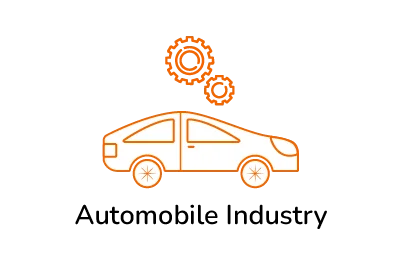
The Magic of Injection Moulding
Streamlining Production for Consistent, High-Quality Parts
Versatility Meets Efficiency
Crafting a Wide Range of Custom Plastic Parts
Mastering Complexity
Handling Intricate Designs and Materials with Ease
From Idea to Reality
Offering Prototyping and Product Development Assistance for Seamless Implementation
Work with us
Step1: Request for Quote
After receive the RFQ, our engineering department will have meeting to study the best solution for the quote, we will provide the quotation according to your request, if we can quote, that means we can make the part perfectly, quotation time within 24 hours
Step2: DFM Report
We can provide the preliminary during the quotation stage if customer request, after order kick off we will make the details DFM for our customer confirmation.
Step3: Mold Flow Analysis
We have our own internal Moldflow team to analysis the part details, we can provide the customer suggestion for part after study the mold flow analysis report.
Step4: Mold Tooling Production
We will strictly check the components dimension make sure all dimension is correct and we will go ahead with the next production, to make sure all components is in tolerance before mold test
Step5:T1 Sample Verification
We will provide the request quantity sample for customer verification, meanwhile we will provide the full dimension report and processing parameter for your reference.
Step6: Low Volume Production
We have from 30t to 1200-ton injection machine in house, we can follow the confirmed sample to manufacture the batch of sample for customer.
Step7: QC Inspection
We can provide the part CMM and 3D scan service inspection. To strictly follow customer provided tolerance drawing to check the actual part.
Step8: Package and delivery
We will provide the different package according to customer transport request, by sea or by air. We will also provide the necessary document to assist our customer make customs clearance.
F.A.Q.
Injection moulding is a manufacturing process used for producing parts by injecting molten material into a mould. It is widely used for making a variety of parts from small components to entire body panels of cars.
Injection molding uses various materials, including thermoplastics (e.g., Polyethylene, Polypropylene, Nylon), thermosetting plastics (e.g., Epoxy, Phenolic ,Urea-formaldehyde), elastomers (e.g., Thermoplastic Elastomers, Rubber), metals (e.g., Aluminum, Magnesium, Zinc alloys), ceramics (e.g., Zirconia, Alumina), and composites (e.g., Glass-fiber reinforced plastics, Carbon-fiber reinforced plastics).
Injection moulding is a manufacturing process used to create parts by injecting molten material into a mould. First, plastic pellets are heated and melted in a barrel. This molten plastic is then injected into a mould cavity under high pressure. Once inside the mould, the plastic cools and solidifies, taking the shape of the cavity. Finally, the mould opens, and the finished part is ejected. This process is highly efficient and capable of producing complex shapes with high precision, making it widely used for manufacturing a variety of plastic products.
A hot runner system is a type of injection moulding setup that keeps the plastic in the runners (channels that lead from the machine nozzle to the part cavities) hot and molten, reducing waste and cycle time.
A cold runner system uses runners that cool along with the moulded part, leading to more material waste, but it’s simpler and less expensive than hot runner systems.
Injection mold design is the process of creating molds for manufacturing plastic parts. It involves planning the mold layout, selecting materials, designing cooling systems, and ensuring easy operation. Good design ensures efficient production of high-quality parts.
Some advantages of injection molding include high production rates, low labor costs, repeatability, minimal material waste, and the ability to produce complex geometries with tight tolerances.
Injection molding involves injecting molten material into a mold cavity to create a part, while 3D printing builds a part layer by layer from a digital design.
Yes, injection molding can be used for prototyping through techniques like rapid tooling or low-volume production runs, providing functional prototypes for testing and validation before full-scale production.
Our injection molding services offer expertise in mold design, material selection, and production optimization, ensuring high-quality parts, timely delivery, and competitive pricing for your project.